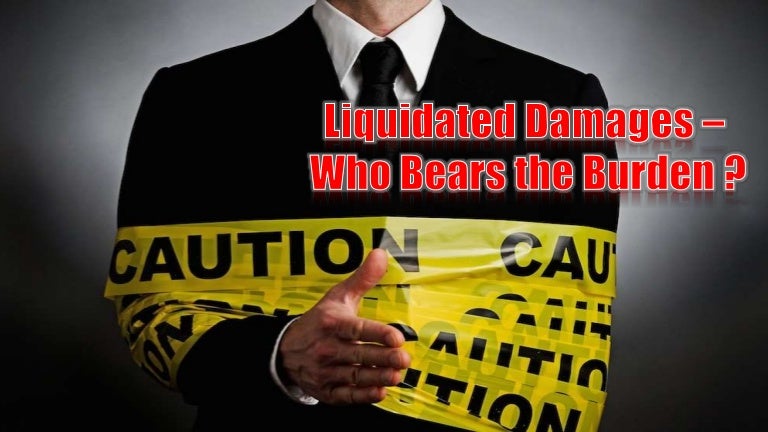
Construction Contracts Hinze Pdf Creator
Sf2 soundfont download. AbstractThe inability of subcontractors/specialist contractors to contribute meaningfully to the construction process under the traditional construction procurement hampers the possibilities of improving value on projects and their integration with the rest of the supply chain. In particular, the main contractors and subcontractors in traditional construction procurement projects pursue their self-interests to such an extent that collaborative working has been impossible to achieve. In this research, qualitative and quantitative approaches were used to collect data to explore the problems at the root of the main contractor-subcontractor relationship.
For courses in Construction Planning and Scheduling and Construction Management. Offering broad coverage of all major scheduling subjects, this book is a comprehensive resource designed for construction management, planning and scheduling. It follows a logical progression, introducing precedence diagramming early and following with chapters on. Download The FREE PDF Converter and create PDF files from any application with PDF Creator. Best of all, PDF Creator is absolutely free for anyone to use. PDFCreator - Download for free, download pdf printer, pdf writer, pdf maker.
Intending to derive innovative ideas to reinvent the delivery process of traditional construction procurement, the principles of integrated project delivery (IPD) and the last planner system (LPS) were studied to seek useful ideas that can be employed to improve collaboration between main contractors and subcontractors. A high point of contention is the debate on the managerial competence of subcontractors; nevertheless, hope is expressed at the possibility of improving collaboration between the main contractor and subcontractor within traditional construction procurement work environment. IntroductionTraditional construction procurement became the main route to procure constructed facilities in the UK soon after the industrial revolution of the nineteenth century , , and to date, it remains the dominant procurement strategy in the UK. It is mostly preferred by one-off clients, who seldom engage in construction. However, in recent times, the use of the traditional construction procurement strategy to procure constructed facilities is falling across the UK. The reason for this decline is because this approach to construction procurement engenders adversarial attitudes , and as a result, conflicts and disputes, poor collaboration, a lack of focus on customers’ requirements, and failure to satisfy clients’ needs have become prevalent in the UK construction industry.Today, construction is so specialised that no one firm can provide all the specialisms; therefore, many small-sized specialist firms (subcontractors) with narrow expertise continue to work to meet the industry’s varied and complex demands.
This situation increases the demand for interdependence of the specialisms and the operating organisations. According to Kale and Arditi , the quality of main contractor-subcontractor relationship affects the main contractors’ ability to perform on projects, which inevitably has direct consequences on project outcomes. This implies that as relationships become more harmonious, there is the possibility of improving the effectiveness and performance of the supply chain since project participants are more able to plan and share resources in an atmosphere of collaboration. But Dainty et al.
realised that subcontractors have some misgivings about the sincerity of the much talked about collaboration of the supply chain. As such, existing relationships particularly between them and main contractors are riddled with mistrusts and scepticisms. They for instance believe that they are merely used by main contractors to improve their cash flow and survive the volatility of the construction business.This problem is made worse by the contractual structure of the traditional procurement route, which excludes subcontractors from the main contract. Morledge argues that the inability of subcontractors and specialist contractors to contribute meaningfully to the construction process under traditional procurement hampers the possibilities of improving value on projects. Specialist contractors and/or subcontractors, as it is well known, play a significant role in the successful delivery of projects, executing between 80 and 90% of the volume of works on building and housing projects – To have this important group excluded from collaborative arrangements in the construction process leaves much to be desired.Owing to their small size and large number, they usually need main contractors to coordinate their operations to provide focus and integration of the varied parts.
However, even with main contractors coordinating, focus on self-interests remains unchanged under traditional construction procurement arrangements, because project delivery processes are still largely disconnected. This leaves room for rivalry amongst project participants, and only the fittest survives. It is the case that, under the traditional approach to construction procurement, contract terms are often so strictly and litigiously applied that little or no consideration is given to sustaining relationships for future business dealings. The desire to seek long term benefits, which comes with collaboration is thus lacking amongst project participants under this approach of project delivery.In an effort to address these challenges, two industry-led and government-commissioned enquiries were undertaken to look into the activities of the UK construction industry. The outcome of these enquires were the Latham and Egan reports. Amongst others, the reports identified that practices within the UK construction industry were inefficient, fragmented, and ineffective. They also revealed that clients’ expectations were not being met and that industry practitioners were making low profits.
The reports therefore called for a change in attitudes and for the integration of project delivery processes in the hope that projects’ successes are improved and that clients are better served.Fragmentation, according to Briscoe et al. , has made the development of a unified approach to project delivery and team continuity between main contractors and key supply chain members difficult over the years.
And on traditionally procured projects, it is blamed for client’s dissatisfaction with completed projects. To improve performance on traditionally procured projects therefore, the work relationships between main contractors and subcontractors needs to change. Regrettably, however, the use of collaborative tools is nonexistent in traditional procurement , and key participants continue to endure and not enjoy their work relationship. Performance ImprovementThe benefits of integrating the supply chain in order to improve project performance have been established in previous studies ,.
It is no surprise therefore that project participants are increasingly realising that sharing knowledge and information is key to project success. Breakdown of responses to question 2—It is easy to employ collaborative tools in traditional procurement.This result however corroborates Eriksson et al. finding that main contractors are not interested in developing cooperative relationships with subcontractors, at least on one-off projects.However, clients show a desire for collaboration to take root in this age-long procurement practice. This demand thus places a burden on construction professionals to yet seek ways of achieving this all important client desire.Construction managers interviewed expressed similar doubts about the possibilities of employing collaborative principles within traditional construction procurement arrangements. They affirm that “it would be very difficult to use because people main contractors are often looking for someone subcontractor to take the risks so that they can maintain their fixed price profit level”, as “ risks are literally sent down to subcontractors”.
They further maintain that “this tendency to transfer risks down the supply chain makes the possibility to collaborate under traditional procurement difficult”. A fact also argued by the interviewees is that “collaboration had worked in framework agreements because they the collaborating companies will all be long-term beneficiaries of that arrangement, but talking of one-off projects, it’s very difficult to collaborate because you wouldn’t want to share a potential loss?”This information indicates that the risk management approach adopted on projects influences the decision to collaborate. For this reason, it is doubtful if subcontractors will collaborate under traditional procurement arrangements knowing that main contractors will transfer almost all of the project risks to them. This disclosure agrees with Bresnen and Marshall’s assertion cited in Eriksson et al. that appropriate project risk management strategy help integrates the supply chain.Amongst a range of factors investigated (see Figure ), the lack of trust ranked highest as the main barrier to integration on construction projects, especially on those procured under traditional construction procurements arrangements.
This is followed by the problem of delayed payments to subcontractors, while the authoritarian practices main contractors employ against subcontractors come third amongst the ranked factors. Although researches by Dainty et al.and Thomas and Flynn have similarly identified some of these factors, they did not unearth the reason for the breakdown of trust. This research establishes a link between the lack of trust and the problem of delayed payments to subcontractors by main contractors. In the view of one of the interviewees, it is because “ prime subcontractors don’t get paid in a timely manner” that trust is eroded.
Factors hindering effective subcontractors-main contractors’ collaboration under traditional construction procurement. Source: Authors’ SurveyMonkey, 2012.Unfortunately, efforts at getting main contractors to deal fairly with their chain of subcontractors have mainly been unsuccessful. Irrespective of the fact that standard contracts stipulate periods within which subcontractor should get paid, those interviewed were unanimous in their opinion that such specified periods are repeatedly ignored, with subcontractors often stretched to the limits before getting paid.
A lot therefore needs to be done to build trust in construction businesses because as Ouchi cited by McDermott et al. found, there is a direct relationship between the level of trust and the costs of transactions, which in turn has effects on clients.The findings of this research similarly indicate that there is a perception amongst some main contractors that subcontractors are not managerially competent. Although this view is not seen to be a significant contributor to the breakdown in relationship, as it is scored the least (Figure ) amongst the list of suggested hindrances to effective main contractor-subcontractor collaboration, further analyses of the result, which is presented in Table, show contrasting main contractors and subcontractors views. The analyses reveal that main contractors’ respondents ranked the fact that subcontractors’ managerial incompetence is a hindrance to effective collaboration at the upper end of the ranking scale. This is perhaps an indication that they doubt subcontractors’ ability to manage projects.
Understandably, subcontractors’ rankings were within the lower end of the scale, suggesting an assertion of their managerial competence. It comes as no surprise therefore that subcontractors complain that main contractors are often reluctant to draw on their expertise when problems occur on site. Comparison of scores given by main contractors and subcontractors to the perceived managerial incompetence of subcontractors as being a hindrance to their collaboration.There is a strong indication from the foregoing that this main contractors’ subtle lack of confidence in subcontractors’ managerial ability leads them to unnecessarily interfere in subcontractors’ operations on site, which has a potential of resulting in conflicts. One such interference an interviewee argues is the many control mechanisms, such as the multilevel approval system, which main contractors have introduced and to which subcontractors must comply. Defending this practice, another interviewee maintains that such controls exist to keep with quality control and assurance requirements.
“It is important to ensure subcontractors undergo checks at every stage of the project before they are cleared to proceed”, he affirms. This statement only serves to confirm complaints that main contractors in the guise of controlling the project under traditional construction procurement assert authority in such a way that they undermine subcontractors’ ability to function effectively and maximise their profits.While the need to keep up to quality assurance requirements is not contested, the use of multilevel approvals (signoffs) to meet standards has unfortunately become the main focus on most sites and fast resulting in an excess of procedures and practices, argues another interviewee. This procedural waste may very well have been avoided or at least substantially reduced with better collaboration between main contractors and subcontractors built on a strong confidence in not just the technical competence of subcontractors, but also on their managerial competence.The lack of confidence between main contractors and subcontractors has turned out to affect the delivery processes of traditionally procured projects in a number of ways. Since the use of common processes is a fundamental collaborative principle, its absence in any project delivery process can only mean chaos. Presently, on traditional construction procurement projects, there is no joint decision process between main contractors and subcontractors. As depicted in Figure, as much as 46% of project participants indicated that they were only occasionally part of the decision making processes on construction sites. Frequency of involvement in decision making.
Source: Authors’ SurveyMonkey, 2012.On further analyses of this result shown in Table, it is immediately apparent that the outcry of none inclusion in decision making processes is a complain predominant amongst subcontractors. Although some main contractors did indicate that they are also left out of decision making processes, this is however doubtful because it is expected that they control the flow of information. The disconnect in sharing information and in the management of construction processes, especially under traditionally procured projects which this investigation reveals, is disturbing regardless of who is making the complaint. This finding contradicts McDermott et al. conclusion that project participants are increasingly realising the benefits of information sharing.
An interviewee sheds light on the reason for the disconnect putting it down to adherence to stereotypes. He argues that “it’s just a culture thing for instance it’s just QSs’ quantity surveyors looking at the upfront cost and seeing it subcontractors’ inputs as a cost rather than as something to add value ”. It also emerged that consultants do not often follow subcontractors’ suggestions for fear of the consequence, should problems arise, and not wanting to be held professionally negligent.
How often project participants take decisions jointly.Other lines of enquiry reveal that not only are subcontractors prevented from decision making processes, but they are more or less also forced to comply. A significant number of main contractors indicate that they allow subcontractors little or no flexibility to debate or challenge their decisions.The results in Figure show that subcontractors are not transparent in their dealings with main contractors.
47% of them admit that they do not inform main contractors of their other projects’ commitments because they either believe it is unnecessary or because they think it will affect the existing work relationship. This practice demonstrates a lack of transparency and does not also encourage collaboration, which further breaks down trust. Informing main contractors about other project commitments—subcontractors’ view. Source: Authors’ SurveyMonkey, 2012.Partners in a work relationship, who are desirous of collaborating, must be open about all of their other work commitments. Concealing such important information has the potential of affecting resource planning and allocation on current projects, thereby hampering work progress.Perhaps a factor which frustrates attempts at employing collaborative strategies within traditional construction procurement in spite of best intentions is the contract of engagement. When main contractors were asked for the reasons for the negative and unfriendly practices that run under this procurement route, they were definite that the nature and conditions of contracts are a key influence.
Indeed, the Institution of Civil Engineers (ICE) and the Joint Contracts Tribunal (JCT) standard forms are notorious for being adversarial, whereas the New Engineering Contract Engineering and Construction Contract (NEC ECC) seeks to have more power swing relationships amongst stakeholders. Confirming this, an interviewee expresses that it is not uncommon to see main contractors treat the same subcontractors differently on the different projects they are both engaged on as it is the contract that determines the flow of things.This research set out to investigate the possibility of employing the collaborative principles of the Integrated Project Delivery (IPD) approach and the Last Planner System (LPS) within traditional construction procurement. But, with the majority of respondents unconvinced about the application of collaborative principles within traditional construction procurement and their quick reference to the nature of contract used under this form of procurement, there is little hope of introducing a single standard form of contract to bind all participants to the client, as used in IPD. However, improvements using the LPS to break down barriers in the main contractor-subcontractor relationship are achievable. LPS’s recognition of construction as a social process and its use in managing relationships makes it a viable tool to reinventing the traditional construction procurement system. Respondents are in agreement on the need for collective planning and production processes, and so useful lessons from LPS, which addresses these issues, can be applied to traditional construction procurement arrangements.The inability of the existing traditional construction procurement contractual structure to encourage collaboration between main contractors and subcontractors is clear.
Coupled with a range of main contractors’ negative attitudes towards subcontractors, the possibility of achieving true collaboration under this construction procurement approach will still take some time to achieve. Nevertheless, to foreclose any possibility for improved collaboration under traditional construction procurement undermines the goal to improve performances in the UK construction industry. ConclusionsThis paper examined some of the relational problems between main contractors and subcontractors, and the practices engendering them have been identified. It established that there is a general lack of enthusiasm between main contractors and subcontractors to adopt collaborative processes within traditional construction procurement projects, which is due largely to the mistrust between them. It revealed on the other hand that construction clients are willing to see collaborative processes adopted, since the majority of them still prefer this route (traditional procurement) to procure their constructed facilities.Amongst other things, the main reasons for the breakdown of trust between main contractors and subcontractors on traditional construction procurement are the issues of delayed payments to subcontractors, disruption to work their plan, their exclusion from decision making processes, and the inclusion of harsh contract terms in subcontract agreements by main contractors. Perhaps the most controversial debate is that which centres on the managerial competence of subcontractors.
These, as well as main contractors’ tendencies to transfer enormous project risks to subcontractors, make a truly relational relationship under traditional construction procurement a wish, rather than a reality. Majority of the research respondents are thus sceptical about the possibility of employing collaborative principles on traditional construction procurement projects. The research found that most of the problems identified above emanate because of the standard form of contract employed in traditional construction procurement.Irrespective of these obstacles, particularly regarding the form of contract in use, this research advocates that these challenges are not insurmountable and there is yet a possibility for participants main contractors and subcontracts in particular to collaborate and overcome their relational problems under traditional construction procurement projects. Looking to more relational procurement strategies, that is, integrated project delivery (IPD) and the last planner system (LPS), proved that collaborations are achievable. An immediate challenge for the introduction of IPD principles in traditional construction procurement is the impracticability of using a single contract to bind all the project participants to the client because of the structure of the procurement strategy.
The possibility of improving relationships within the procurement strategy, using the ideologies of LPS, remains very much achievable.This offers some hope that the UK’s traditional construction procurement approach to project delivery can indeed be reinvented. LPS’s adaptability to any standard form and its applicability to address waste, delays, and lack of coordination in construction processes means it will not only breakdown adversarial tendencies known with traditional procurement, but will ensure commitments on projects, thereby allowing collaborative programming and production planning decisions to be more easily made. This claim however needs further practical verification. A suggestion for future research should seek the practical application of the Last Planner System’s five conversations within a traditional construction procurement environment to ascertain the veracity of the claim reached in this research that its application within traditional construction procurement will improve collaboration between main contractors and subcontractors.Finally, true collaboration within traditional construction procurement supply chain is only achievable if parties commit to the ideals of collaboration.
They must seek not only to transact but to relate in order to build trust. Main contractors and subcontractors in particular must be ready to place some of their profits at risk, rather than seek to reap rewards at each other’s expense. References. S. Rowlinson and P. McDermott, Procurement Systems: A Guide to Best practice in Construction, E & EN Spon, London, UK, 1999.
Jones, and P. James, “A review of the progress towards the adoption of supply chain management (SCM) relationships in construction,” European Journal of Purchasing and Supply Management, vol. 173–183, 2002. View at:. RICS, Survey of Building Contracts in Use During 2007, The Royal Institution of Chartered Surveyors, London, UK, 2007.
CIOB Chartered Institute of Building, Procurement in the Construction Industry, CIOB, West Berkshire, UK, 2010. Yu, “Coordination mechanisms for construction supply chain management in the Internet environment,” International Journal of Project Management, vol. 150–157, 2007. View at:.
P. Nilsson, and B.
Atkin, “Client perceptions of barriers to partnering,” Engineering, Construction and Architectural Management, vol. 527–539, 2008. View at:. J. Bennett and D. Ferry, “Specialist Contractors: a review of issues raised by their new role in building,” Construction Management and Economics, vol.
521–532, 1990. View at:. S. Arditi, “General contractors' relationships with subcontractors: a strategic asset,” Construction Management and Economics, vol.
541–549, 2001. View at:. A. Briscoe, and S. Millett, “Subcontractor perspectives on supply chain alliances,” Construction Management and Economics, vol. 841–848, 2001.
View at:. D. Tommelein and G.
Ballard, “Coordinating specialists,” Journal of Construction Engineering and Management (ASEC), pp. View at:. R. Morledge, “A review of the value of the main contractor,” in Proceedings of the Construction and Building Research Conference of the Royal Institution of Chartered Surveyors (COBRA '08), London, UK, September 2008. View at:.
D. Arditi and R. Chotibhongs, “Issues in subcontracting practice,” Journal of Construction Engineering and Management, vol. 866–876, 2005. View at:. J.
Hatmoko and S. Scott, “Simulating the impact of supply chain management practice on the performance of medium-sized building projects,” Construction Management and Economics, vol. View at:. K. Hampson and T. Kwok, “Strategic alliances in building construction: a Tender evaluation tool for the public sector,” Journal of Construction Procurement, vol. View at:.
J. Tracey, “Contractor-subcontractor relationship: the subcontractor's view,” Journal of Construction Engineering and Management, vol.
274–287, 1994. View at:. O. Matthews and G. Howell, “Integrated project delivery an example of relational contracting,” Lean Construction Journal, vol.
View at:. S. Latham, Constructing the Team: Final Report of the Government/Industry Review of Procurement and Contractual Arrangements in the UK Construction Industry, HMSO, London, UK, 1994.
Egan, Rethinking Construction: The Report of the Construction Task Force on the Scope for Improving the Quality and Efficiency of UK Construction, HMSO, London, UK, 1998. Wolstenholme, Never Waste a Good Crisis: A Review of Progress Since Rethinking Construction and Thoughts for Our Future, Constructing Excellence, London, UK, 2009. Dainty, and S. Millett, “Construction supply chain partnerships: skills, knowledge and attitudinal requirements,” European Journal of Purchasing and Supply Management, vol.
243–255, 2001. View at:. P. Eriksson and A.
Laan, “Procurement effects on trust and control in client-contractor relationships,” Engineering, Construction and Architectural Management, vol. 387–399, 2007. View at:. P.
DescriptionMeasurement is an essential activity in every branch of technology and science, the fourth edition of this successful text has been extensively extended and updated to include new developments in measurement devices and technology.Principles of Measurement Systems, 4/e provides a coherent and integrated approach to the topic, covering the main techniques and devices used, together with relevant theory applications, for both mechanical and electronic systems. Bentley jp principles of measurement systems pdf download.
Dickinson, and M. Khalfan, “The influence of partnering and procurement on subcontractor involvement and innovation,” Facilities, vol. 203–214, 2007. View at:. P. McDermott, M.
Khalfan, and W. Swan, “An exploration of the relationship between trust and collaborative working in the construction sector,” Construction Information Quarterly, vol. 140–146, 2004. View at:.
M. Bresnen and N. Marshall, “Partnering in construction: a critical review of issues, problems and dilemmas,” Construction Management and Economics, vol. 229–237, 2000. View at:.
Constructing Excellence, “Partnering in Practice. Construction Excellence,” 2004,. View at:. Constructing Excellence, “Supply Chain Partnering. Construction Excellence,” 2004,. View at:.
L. Clarke and G. Herrmann, “Cost vs. Production: disparities in social housing construction in Britain and Germany,” Construction Management and Economics, vol. 521–532, 2004. View at:.
J. Hook, “Industry issues. View at:. L. Chuan, “Just-in-time management in precast concrete construction: a survey of the readiness of main contractors in Singapore,” Integrated Manufacturing Systems, vol. 416–429, 2001.
View at:. H. Thomas and C. Flynn, “Fundamental principles of subcontractor management,” Practice Periodical on Structural Design and Construction, vol. 106–111, 2011.
View at:. E. Johansen and G. Porter, “An experience of introducing last planner into a UK construction project,” in Proceedings of the 10th Annual Conference of the International Group for Lean Construction, International Group for Lean Construction, Virginia, Va, USA, July 2003. View at:. A.
Kadefors, “Trust in project relationships-inside the black box,” International Journal of Project Management, vol. 175–182, 2004. View at:. N.
Proverbs, and Y. Debrah, “Factors influencing the culture of a construction project organisation: an empirical investigation,” Engineering, Construction and Architectural Management, vol. View at:. A. Mignot, “Alliancing benefits and challenges in infrastructure projects. Project Manager,” 2011,.
View at:. A. Ireland, and M. Townsend, Managing in Construction Supply Chains and Markets, Thomas Telford, London, UK, 2006. Leicht, “Initiating IPD Concepts on Campus Facilities with a “Collaboration Addendum”. Construction Research Congress 2012 ASCE,” 2012,.
View at:. R. Vrijhoef and L. Koskela, “Roles of Supply Chain Management in Construction.
Proceedings of the Seventh Annual Conference ofthe International Group for Lean Construction(IGLC-7) Berkeley, Calif, USA,” 1999,. View at:. G. Ballard, “Improving Work Flow Reliability. Proceedings of the Seventh Annual Conference of the International Group for Lean Construction (IGLC-7 ) Berkeley, Calif, USA,” 1999,.
View at:. R.
Mossman, and S. Emmitt, “Lean and integrated project delivery. Special Issue,” Lean Construction Journal, pp. View at:. A. Mossman, “Last Planner: collaborative conversations forpredictable design & constructiondelivery. The Change Business Ltd,” 2012,.
View at:. A.
Bryman, Social Research Methods, Oxford University Press, New York, NY, USA, 3rd edition, 2008. Ho, “Partnering in construction: critical study of problems for implementation,” Journal of Management in Engineering, vol. 126–135, 2003. View at:. A. Oladapo, “An investigation into the use of ICT in the Nigerian construction industry,” Electronic Journal of Information Technology in Construction, vol. 261–277, 2007.
Whether you’re using them for business, school, or general use, PDF files are a fantastic way to share information. In this article, we’ve collected the best free PDF editors you can download today.Whether you’re using them for business, school, or general use, PDF files are a fantastic way to share information. The great thing about PDF documents is that their content doesn’t change no matter what kind of program you use to open them or what device you’re viewing them on. This makes PDF documents ideal for important information that could be open to misinterpretation if the document’s style or formatting was changed.The one problem is that there aren’t very many free PDF editors. This is because Adobe, the original creator of the PDF format, actually still owns some technologies associated with it. Adobe charges software manufacturers a fee for working with PDFs which is why most programs can save documents in the PDF format but can’t edit them.Because there aren’t all that many free PDF editors out there, it can be challenging to know which is the right one to use.
That’s why we decided to put together the definitive list of the best free PDF editors, which you’ll find below. The best free PDF editors at a glance. Limited free trialWith Smallpdf’s Edit PDF tool, you get a simple user interface that allows you to add text and image content to your PDF files.
This platform also offers simple e-signing, and the ability to add comments and highlights to information already stored in your PDFs.The Smallpdf system actually contains lots of other PDF modification tools too. Along with the editor function, there’s a variety of options to convert PDFs into easier-to-edit formats such as Word and Powerpoint files, and you can save space by merging individual PDF documents into a single file.But the best thing about Smallpdf is that it’s a cloud-based platform. In other words, you can access it from any supported device simply by visiting the Smallpdf website and dragging-and-dropping a PDF into your browser.Don’t be thrown off by the prompts to begin a 'free trial' – you only have to do that if you want to install the Smallpdf Desktop program for offline editing.Read our full2. PDF-XChange Editor. Watermarks documentsPDF-XChange Editor is a free PDF editing program for Windows computers developed by Tracker Software. The interface is a little more complex than that of the Smallpdf editing suite but gives you easy access to plenty of helpful features such as a stamp option for marking documents as 'Expired' or 'Approved'.But for most users, the main reason to use PDF-XChange Editor is the fact that it comes with inbuilt Optical Character Recognition (OCR).
This means that if your original PDF document is a photocopy, PDF-XChange will still recognize the text and allow you to edit it. Also, PDF-XChange Editor lets you reformat text, and even convert it into fonts that aren’t already loaded on your computer.And like Smallpdf, you can use this platform to merge or split individual PDF files. The only serious downside of this powerful editor is that, if you haven’t signed up to the Pro version, a small 'Created with PDF-XChange Editor' watermark will be added at the bottom of any PDF files that you export.Read our full(Image credit: KingStreetLabs; Shutterstock) 3. Can't split/merge documentsFormSwift is an in-browser PDF editor that you can start using in just a couple of seconds.
Unlike PDF-XChange Editor and Smallpdf, the FormSwift platform is totally free. That means there’s no need to start a free trial to use it.

There aren’t even any annoying 'upgrade now' prompts to ignore.With support for image addition, text editing, e-signatures, and checkmarks, FormSwift has everything you need to perform basic PDF edits. After you’ve finished your edits, you can print directly from the FormSwift interface or save your file as a Word or PDF file.Plus, if you need to import a paper document for editing, all you need to do is visit the on your phone. Once you’ve given it permission to, the platform will use your phone’s camera to import the file.Full FormSwift review coming soon4. Desktop editor is paid-onlyWith PDFescape, you can either edit online or through a desktop application. The desktop application is the more powerful of the two as it supports edits to pre-existing PDF content and allows you to scan paper documents. However, only the online version of PDFescape is free to use.All the same, you get plenty of useful PDF editing options with PDFescape online such as the ability to make freehand notes and a tool for adding clickable URL links to your documents.
You’ll also find that it’s pleasingly easy to add, rotate, and annotate pages with the in-browser version of PDFescape.The only major flaw of this free PDF editor is that you can’t upload documents that are larger than 10MB. A regular A4-size PDF page only takes up about 100KB of data though, so this shouldn’t cause a problem unless you’re editing a book-length document.Read our full5. Premium is expensivePDF files are a good way to store professional or financial information, which means that their contents are often sensitive.
Sejda is a free online PDF editor that you can trust with important documents because all uploaded files are wiped from its servers after five hours.Aside from security, Sejda is a good choice if you are after a free PDF editor with a user-friendly interface. Sejda’s single menu bar makes it easy to find all the editing options necessary for adding text, links, images, and signatures to PDF documents.When you’re done editing a document in Sejda, you just need to click the 'Apply Changes' button and proceed to save the finished product in your Google Drive account, Dropbox system, or locally.Sejda does come with some limits, but they aren’t restrictive enough to cause problems for casual users. You can only perform three tasks and upload 50MB, or 200 pages of information to the Sejda platform every hour.Read our fullWhich type of free PDF editor is best for you?When deciding which of the free PDF editors below to download and use, first consider which bits of your PDF file you need to change. If you’re just trying to add your information to a form digitally, you’ll just need a basic editor that supports text insertion.However, if you need to change the content of a PDF substantially, you’ll require a more powerful PDF editor that can make modifications to text or images already stored in the file. In some cases, especially if you want to change almost all the content of your file, it may be better to use a converter program instead. Check out our guide to the best.